Contingency planning on a business transformation project often feels like a Catch-22: people don’t want to do contingency planning because there’s a superstition in admitting that the best laid plans could fail or that there are actual risks that can impact the go-live or business ramp-up.
But by not coming up with contingency plans, those very same ignored risks are only more likely to have a major impact at go-live. Keeping in mind the uncomfortable truism of Murphy’s Law that anything that can go wrong inevitably will, it’s generally a better approach to be over-prepared and underwhelmed rather than be under-prepared and overwhelmed.
Issues will inevitably arise that end up impacting or even slowing down certain aspects of business operations or project progress. At that point, it’s too late to plan for contingencies because they’ve already happened and all you have left is improvisation and heroics. But there is a better way.
Contingency planning is all about creating controls to help manage and reduce risk by creating and rehearsing multiple rapid recovery or alternate methods. The focus is on key activities and likely failure points that have the most risk and largest impact on business operations.
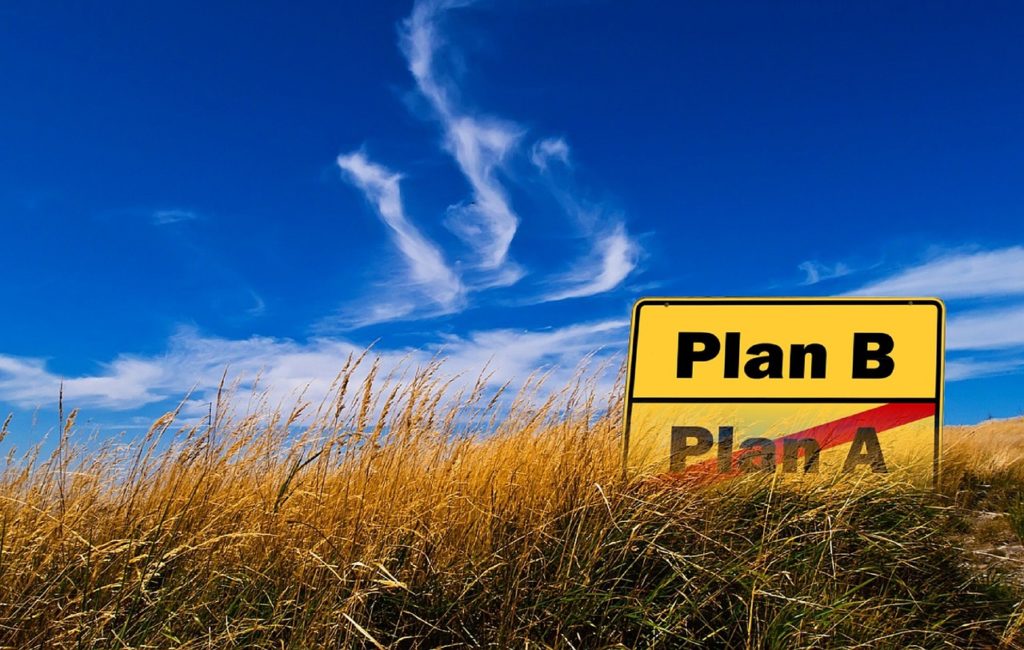
An Illustration: How Contingency Plans Work in Action
Here’s an example of how effective a contingency plan can be at mitigating issues.
I was on a project where the leadership team was already aligned to a contingency plan and had it in play (a rare occurrence, unfortunately). As part of that plan, it was agreed that no inventory would be moved during the final cutover from the old system to the new, as any difference between where the product was in reality versus where it was reflected in the system would cause disruption during business go-live and ramp-up. A further part of the plan implemented checks and balances reports to help identify if inventory was somehow physically moved.
Just imagine the headache: you need to ship a product, so you go to the shelf where the system tells you that item is stored, only to find a completely different product in its place; now multiply that problem by a factor of a thousand.
Well, as Murphy’s Law predicted, there were decisions made near go-live to physically move the inventory within the warehouse to generate some cost ratio benefits per square foot. This inevitably led to the aforementioned disruption during go-live, since the inventory was out of sync between systems and physical locations, which caused the warehouse team to require additional time to reconcile, make inventory adjustments, and map to the new location.
Fortunately, the contingency plan kicked in and the reports were generated and analyzed to proactively identify the required physical to system adjustments. With support from resources that were able to review and validate the inventory adjustments required, the process was expedited without a hiccup.
The lesson here is that by having a contingency plan for this eventuality, we were able to save precious time during the go-live weekend. Although we had some minor delays with the system release, we were still able to avoid days or weeks of delays that would have occurred had there not been a clear plan on how to correct the inventory location accuracy issue.
Challenges to Contingency Planning
Even if you’ve decided to invest resources in contingency planning, effectively completing the exercise can be difficult. Here are some of the bottlenecks and disruptions that can occur, as well as how to overcome them.
Challenge #1: Everyone Wants to Be a Priority
Every team will feel its area of focus and processes are critical, which will make it challenging to get alignment on the scope of contingency planning. Who do you prioritize? Who gets a say?
Some areas of the project may indeed have a large number of risks. It’s up to you and the contingency planning team to sort through and identify which are truly likely to materially impact the business as a whole—for example, direct customer impacts— and focus on planning mitigations for those areas.
How to Manage Competing Priorities: Take a risk-based approach. Start assessing risks early and iterate often to get to the truly important ones. Have regular contingency planning cycle milestones integrated into a project’s critical path plan to maximize the team’s focus throughout the lifecycle of the project.
Challenge #2: Lack of Follow-Up
Another issue can occur when the risks you’ve identified are not followed up consistently to close or mitigate them through the project lifecycle. People agree the risk exists and agree that it should be closed but then get distracted. A more insidious variety of this challenge is when an old risk is closed but the solution itself creates a new and different risk that hasn’t been considered. Here you have the problem of either having an outdated picture of what the nature of your risk is, or not even realizing that a wholly new and different risk has come about.
Similarly, lack of follow-up can manifest itself in actual lack of mitigation plan training. Once a mitigation, or sometimes more aptly referred to as a “scramble plan”, is identified to handle a given failure point, everyone nods and goes about their day without preparing, training the extended teams, or even properly documenting how the folks on the ground need to scramble. When the day comes to have to activate the contingency no one is even quite sure what to do.
How to Avoid Half Baked Plans: Clearly identify resources with accountability and responsibility who will own any follow-ups involved in contingency planning, whether to close risks or prepare to use the contingency plans. Here again, multiple iterations and relentless reassessments are instrumental to ensure plan accuracy and associated follow-up activities completeness.
Challenge #3: Leadership Isn’t Fully on Board
Be on the lookout for limited buy-in and support from leadership and stakeholders, as for the plan to be effective, it’s imperative to have support from the leaders who will be needed to rally the teams to perform the activity. All hands on deck! If leadership believes that contingency planning is a result of poor project execution rather than a sign of best practices to project health, it’s your job to communicate the importance and explain how it can keep issues from arising down the road.
How to Convince the Boss: Clarifying where contingency planning fits in with the overall project plan will make leaders and stakeholders more amenable to the idea if they understand why it is required. Be ready to answer “what’s in it for us” to prove the value of the plan. Last but not least, remember to continue educating the leaders that, beyond having a handy Plan B in the event things go wrong, the contingency planning exercise itself helps the teams to consider what could go wrong so as to prevent it. As a last resort, just send them this article.
Challenge #4: Team Members Aren’t Motivated
With team members involved heavily in the day-to-day of getting the project to go-live, you may find it difficult to motivate them. They may not have the time or focus to come up with a Plan B since they’re putting significant time into all the Plan A activities.
How to Light the Fire: Communicate frequently to ensure alignment with task owners to drive the contingency plan creation and review accountability for team members. Make people comfortable by assuring them that the team is doing all it can to ensure Plan A will be successful, but in the event of an issue where Plan B may need to be invoked, you have a plan for how the teams will operate and execute.
The impact of an outage with no workaround plan can negatively impact a project timeline, relationships with customers, and, in certain industries such as medical device manufacturing, can impact human lives. You cannot plan for everything, but you can help mitigate risk for high-impact areas by developing a proactive strategy based on thought processes against disruptive events that might occur.
Share: